Lunchtime talk write-up
Posted on Mon 21 Dec 2015
Making in China with Molly Price and Fiona Dowling
On Friday 11 December, Molly Price and Fiona Dowling joined us to share their recent experiences exploring Maker culture in China. Molly is a designer, maker and Studio resident and Fiona is the founder of The Laser House.
Molly Price
Speaker
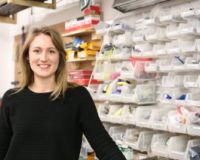
Molly Price
Molly is a designer and researcher with a background in architecture and site-specific interactive art. She has developed specialism in smart textiles and wearable technology through research and collaboration to create designs that aim to connect people with their environment in new and meaningful…On Friday 11 December, Molly Price and Fiona Dowling joined us to share their recent experiences exploring Maker culture in China. Molly is a designer, maker and Studio resident and Fiona is the founder of The Laser House. Here are five things I learned:
1. British Council sent nine makers and academics to Shenzhen, on the west coast of China to research Maker culture and how the increase in manufacturing costs is driving factories inland. The Chinese government has started to recognize the value in design and innovation and is steering towards supporting makers to innovate in a move against the well-established culture of cheap mass production.
2. Molly and Fiona observed three types of makerspaces in Shenzen, and unlike in the UK, the term ‘makerspace’ is also broadly used for co-working spaces. The three types are:
- Government funded: these spaces are new and well equipped, generally akin to western makerspaces. Most are tailored towards electronics and industrial design. To join a space, makers must apply to a panel.
- Community led: these spaces appear more well used and host a diversity of making practices. They request minimal membership fees, and are insulating their communities from government pressure to rapidly produce products.
- Educational: these spaces host interactive media arts courses, as well as after school clubs. Children have to opportunity to learn the making process from concept through to fundraising and prototyping.
3. Downstairs from many Shenzhen makerspaces you will find large markets for electronic component parts; this immediate accessibility, which is rarely available in the UK, provides the tools for rapid product prototyping. Alongside this, there are companies such as Seeed Studio who are working towards bridging the gap between makers and factories. Developing a maker-friendly supply chain, which allows makers to order their products in low numbers, is key to developing the shift in focus to design and innovation.
4. Molly is developing a smart textiles product that involves engaging with textiles and electronics manufacturing companies simultaneously. In addition to the challenges brought about by the factories operating far apart geographically, communication lines between these supply chains was difficult. There seems to be little precedent in Shenzhen for smart textiles or wearables, so producing a soft technology product requires a high level of communication integration between the two industries.
5. The majority of manufacturers and makers who Molly and Fiona worked with spoke English, however the subtleties involved in communicating detailed design aspects did create a language barrier. Molly and Fiona recommended for UK makers and designers to visit Shenzhen and meet with manufacturers face-to-face. With the ready access to component markets, efficient and local factories and companies dedicated to streamlining the supply chain, products can be accelerated from prototype to production ready very quickly.
You can find out more about the Living Research: Making in China project by visiting the British Council blog.