Posted on Sat 3 Mar 2018
Fabrication & Narrative
Interface/physical design and user experience
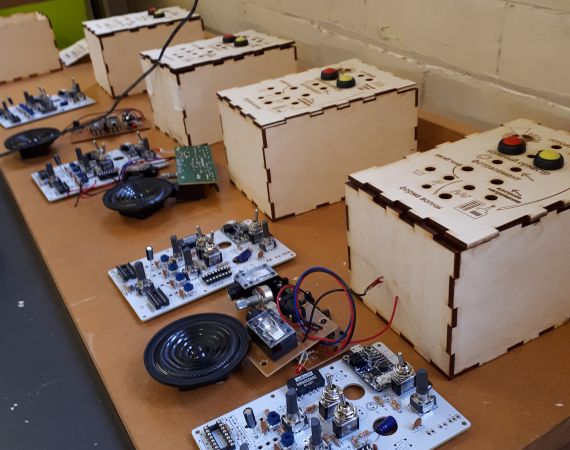
Posted by
Project
As part of the audience experience, we wanted to provide a narrative hook for the participants who would be using the machines in our sound walk. We decided to tell people that our machines were in fact abandoned soviet technology from the 1920s, that we had been researching and investigating the original purpose for this technology and discovered it was a way of measuring and interrogating the light in cities (with the coming of Russian electrification ) through noise. We imagined an alternative existence where sonic culture had become the dominant culture and sense over the visual, the very antithesis of ‘occularcentrism’, where sound was the medium of measurement.
Having finalised our circuit design, we worked with The Invent Hive who supported us in the schematic layout and final PCB design (thank you), ready to be sent to manufacture, we eagerly awaited their return for first tests.
The start of January was our residency at Fondazione Mondo Digitale in Rome, a well resourced fablab, wonderful art, technology and education centre leading on Rome Media Art Festival. Our focus for this stage was designing the control panel and interface for the machines.
As a nod to the Russian futurists we decided that any normal text or labels on the control panel would be written in cyrillic. We knew this would be indiscernible to most participants, but this was intentional to fit with our ‘abandoned soviet technology’ narrative. This tactic had some interesting outcomes which will be discussed in the next blog post.
Following Rome we headed straight to BBC Media City in Salford! Working at Eagle Labs to develop the 3D printed speaker section for our sculptures. The detail and level of precision that went into aligning our PCB, components, Control panel interface and speaker section were crazy, but we somehow managed to get all these parts synced for them to work as prototypes for the first festival walk.
Working with 3D print was an interesting experience. Our intention and design was that the entire machine sculpture would be 3D printed to house the electronics. However we found that each machine would take up to 25 hrs to print, with the SPECTRA Festival deadline looming and limited time, we had to opt for plan B, to 3D print the speaker chamber and house the electronics in bespoke wooden enclosures. It was a race to the finish, with marathon soldering days to complete the 10 machines in time for their first outing at SPECTRA Festival.